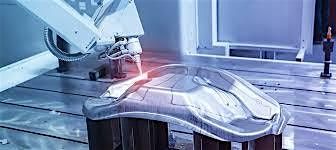
About this Event
Develop / review a company's Master Validation Plan for major cGMP deficiencies. Address the U.S. FDA's newer and tougher regulatory stance. One major failing is lack of sufficient or targeted risk-based V&V planning:
- Start with a Master Validation Plan;
- Evaluate its elements against ISO 14971 and ICH Q9 for hazard analysis and product risk management;
- The Individual V&V Plan;
- V&V Project Management;
- “Risk-based” per ISO 14971, ICH Q9, and/or GAMP/JETT;
- Two key input analysis tools;
- Change control and “drawing a line in the sand”;
- Develop meaningful V&V Files and Protocols for:
- Products;
- Process;
- Production Equipment;
- Monitoring and Test Equipment;
- Software;
- Quality Management System – 21 CFR 11, Electronic Records / Signatures;
- The roles of different V&V protocols;
- How to employ equipment / process DQs, IQs, OQs, and PQs, or their equivalents,
- V&V against a background of limited company resources;
- The FDA's 11-element software matrix simplifies "as-product", in-product", process and equipment, et al, software VT&V
- Assure key U.S.FDA and comparable EU MDD / ISO requirements are not overlooked;
- The QMS and 21 CFR Part 11, “Electronic Records / Signatures” V&V
- Hands-on examples and activities show real-world implementation of useful principles, tools and templates;
Learning Objectives
- Understand Verification and Validation, differences and how they work together
- Develop a “Working Definition” of V&V, Qualification, and related terms
- Discuss recent regulatory expectations
- How to document a “risk-based” rationale, and use it in a resource-constrained environment
- Determine key “milestones” and “tasks” in a project; device sample provided
- Locate and document key subject “inputs”
- Compile “generic” Master and Individual Validation Plans
- Lean the key element of a Product V&V File / Protocol
- How to develop Process and/or Production / Test Equipment V&V Files / Protocols
- Basic Test Case / Script construction
- Sample sizes and their justification
- Lean the key 11 elements of Software V&V expected by the FDA and how to document
- See how to compile QMS Electronic Records and Electronic Signatures V&Vs per 21 CFR 11 and related CGMPs
Agenda
Session Start Time: 12:30 PM
- Introductions; Housekeeping Announcements; Workbook Walk-Through
- V&V Planning; The Master Validation Plan; The Individual Validation Plan
- Break and Q & A
- “Risk-based” -- Evaluate its elements against ISO 14971 and ICH Q9 for hazard analysis and product risk management – File Narrative, Hazard Analysis, FTA, 3 FMECAs (Design, Process, Use[r], and a possible 4 th , Software); also GAMP / JETT approaches
- V&V Project Management – “Milestones” and “Tasks”
- Two key input analysis tools – The Process Map / Flow Chart, and the Cause and Effect Diagram (templates supplied)
- Change control and “drawing a line in the sand”
- Break and Q & A
- Elements of a V&V File / Protocol:
- Intro / Purpose / Scope
- Protocol Material / Equipment
- DQ or Requirements Specs
- ASTM2500
- IQ (or equivalent)
- OQ (or equivalent)
- PQs (or equivalent)
05:00 - Day One Wrap-up
<h4>Day 2</h4>Session Start Time: 12:30 PM
- Develop and Employ Meaningful V&V Files and Protocols for:
- Products;
- Process;
- Production Equipment;
- Monitoring and Test Equipment;
- Software;
- Quality Management System – 21 CFR 11, Electronic Records / Signature
- The FDA’s 11-element software matrix simplifies "as-product", in-product", process and equipment software V&V – what they mean, how to research and how to document
- The QMS, ERP and 21 CFR Part 11 V&V – “Cloud” Issues; “White box” and “Black box” Testing; Basic Test Case Development
- V&V, Senior Management / IP and Limited Company Resources
- U.S. FDA Audit Issues and “Responsible” Documentation
- Course Highlights and Q & A
Who will Benefit
This seminar will provide valuable assistance to all regulated companies that need to review and modify their Master Validation Planning and Plan(s). While this information is focused on Medical Devices, its principles apply to personnel / companies in the Pharmaceutical, Diagnostic, and Biologics fields. The employees who will benefit include:
- Senior and middle management and staff
- Regulatory Affairs
- QA/QC
- IT/IS
- R&D
- Production Management
- Manufacturing Engineers
- Process Engineers
- Software Engineers
- Project Managers
- Hardware and software vendors, sales and marketing
- Faculty John E. Lincoln
Medical Devices / Regulatory Consultant; also pharma and dietary supplements
Saint George, Utah
John E. Lincoln is Principal of J. E. Lincoln and Associates LLC, a consulting company, with over 32 years experience in U.S. FDA-regulated industries, 18 of which as a full time independent FDA-regulated industry consultant. Mr. Lincoln has worked with companies from start-up to Fortune 100, in the U.S., Mexico, Canada, France, Germany, Sweden, China and Taiwan. He specializes in quality assurance, regulatory affairs, QMS / CGMP audits and problem remediation and FDA responses, new / changed product 510(k)s, process / product / equipment including QMS and software validations, ISO 14971 product risk management files / reports, Design Control / Design History Files, Technical Files. He’s held positions in Manufacturing Engineering, QA, QAE, Regulatory Affairs, to the level of Director and VP (R&D).
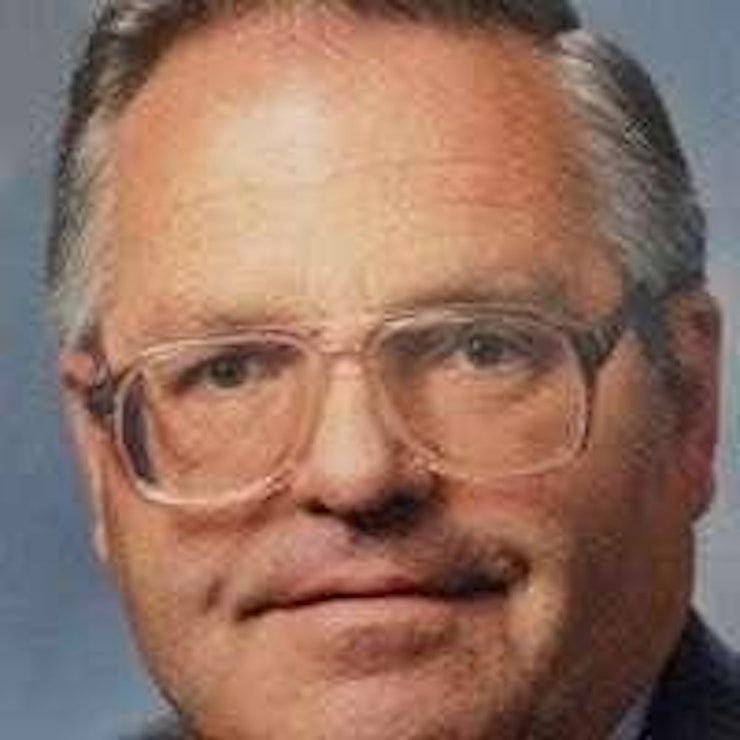
Event Venue
Online
USD 1495.00 to USD 3999.00